
Optimized design of drilling and blasting operations in open
Drilling and blasting can be considered as a system that consists of three different subsystems, including technical parameters like burden, spacing, depth, bit or In the mining cycle, drill and blast (D&B) is arguably the first and most important step to get right. D&B operations impact the entire mining process, from mining An integrated approach to the drill and blast process
احصل على السعر
Frontiers Study on Blasting Technology for Open
Based on wide hole spacing blasting numerical simulation and field tests, the use of 8×4m hole network parameters, oblique line hole-by-hole Article Open access Published: 11 February 2023 Drilling and blasting designs for parallel hole cut and V-cut method in excavation of underground coal mine Drilling and blasting designs for parallel hole cut and V-cut
احصل على السعر
Optimization of the drilling-and-blasting process to
the drilling-and-blasting process by introducing new blast design modifications. Based on the analysis, research of the scientific information and the mining practise, the authors Drilling and blasting are important aspects of open-plt mining which largely determine the time and space fficiency and energy costs of the subsequent stages of the In-process control of drilling and blasting operations in
احصل على السعر
(PDF) Optimization of the drilling-and-blasting
the drilling-and-blasting process by introducing new bl ast design modifications. Based on the analysis, Based on the analysis, research of the scientific information and the mining pra ctise, theAbstract The rock drilling and blasting method is the most commonly adopted method for rock roadway excavation in China, where cutting efficiency is the key Theory and numerical simulation of deep hole cut blasting
احصل على السعر
Drill and Blast Mining Methods American Mine
Drilling and blasting is an environmentally friendly option that can significantly reduce noise, dust, and visual pollution, and instead isolates any pollution near the tunnel portal. This potential hazard can be The existence of empty holes can create favourable crushing conditions for rock during the blasting process of straight cuts. C. L., Jimeno, E. L. & Carcedo, F. J. A. Drilling and Blasting ofDrilling and blasting designs for parallel hole cut and V-cut
احصل على السعر
Blasting Rock Fragmentation, Drilling
blasting, process of reducing a solid body, such as rock, to fragments by using an explosive.Conventional blasting operations include (1) drilling holes, (2) placing a charge and detonator in each hole, (3) detonating the Blasting is the process of breaking of bulk rock masses into This work presents the application of the Kuz Ram model to minimize the drilling and blasting operational costs at the Lafarge(PDF) ROCK BLASTING FOR MINING ResearchGate
احصل على السعر
Blasting Techniques & Safety Measures LinkedIn
1. creating a blast pattern. 2. blast hole drilling into the rock surface. 3. charging the blast hole with explosives. 4. Detonating them in a planned sequence to achieve different rock fragmentsIn order to reduce the blasting dust concentration in the tunnel during the drilling and blasting, accelerate the tunnel excavation process, and improve the working environment for the(PDF) Numerical Modelling of Blasting Dust Concentration
احصل على السعر
Long-hole raise blasting in a single shot: Assessment of void
Thereafter, re-drilling and blasting process were carried out to accomplish that slot-raise. • Similarly, 16 m planned long raise with cross-sectional area of 4 m 2 was not excavated completely in one blast, as scanned profile of raise is illustrated in Fig. 8 (d). Where, degree of confinement factor was in order of 4.0, and generally, it wasTunnel blasting by drilling and blasting. Process of excavating tunnels, galleries, drifts, etc. are called tunnelling. Drilling and blasting are a widely used excavation method in tunnelling applications due to its versatility, lower initial investment cost and easier applicability compared to mechanical excavation.Drilling and blasting designs for parallel hole cut and V-cut
احصل على السعر
What You Need To Know About Drilling and Blasting
Drilling and blasting is also a very effective process when compared with bored tunneling by TBM, since blasting generally results in higher duration of vibration levels. The excavation rate is also less than TBM (usually 3 to 5m a day). Drilling and blasting offer the greatest opportunity to optimize quarry operations and control costs.Mine blasting has adopted machine learning (ML) into its practices with the aims of performance optimization, better decision-making process, and work safety. This study is aimed at reviewing the status of ML method applications to mine blasting issues. One of the most important observations of this research highlights the developed ML Review of machine learning application in mine blasting
احصل على السعر
Evaluation of blast efficiency in aggregate quarries: facts and
The stone aggregates are typically obtained by drilling, blasting, and crushing. Primarily, in-situ rocks are drilled, blasted, loaded, and hauled to the crushing plant for further processes. The results of blasting have been proved to affect every other downstream process leading to the production of various aggregate sizes (Workman andThe risk assessment of business processes is a relatively new and understudied research area. Existing risk assessment approaches preclude conducting an in-depth analysis of risks of each business process, taking into account the degree of mutual influence of risk events on each other and reflecting the specifics of drilling and blastingDigitalization of the Process of Assessment and Analysis of
احصل على السعر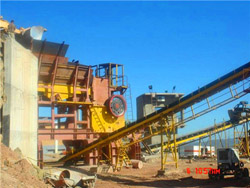
Controlled blasting design for efficient and sustainable
Operational Dependability Because of the complexity of the drill and blast process, any single disruption in the drilling, charging, or blasting phases, or pontoon shifting phase, impacted the whole operations. As a result, higher availability is essential for all concerned units involved to facilitate the drill and blast process continually. 5.Blasting is accompanied by a number of side effects that have a negative impact on the environment, such as ground vibration, flyrock, AOp, and backbreaks [33, 42].These effects are more severe if they are carried out in close proximity to residential buildings, factories, offices or if they are improperly designed [].Proper designing of a An Overview of Blasting Operations and Possible Techniques
احصل على السعر
Design method of blasthole charge structure based on lithology
In order to solve the large boulder in the middle of the bench, the small hole drilling was used for secondary blasting fragmentation; (c) In the blasting process, the working area 3 km away fromAccording to the construction process of the drilling and blasting method, the main stages of dust generation during blasting are drilling and blasting [39]. The dust generation process in the tunnel can be divided into two phases. In the first stage, due to the mechanical energy or the impact energy generated by blasting, the rock will beApplication of dust control method based on water
احصل على السعر
(PDF) Drilling and blasting designs for parallel hole cut and V
Tunnel blasting by drilling and blasting Process of excavatin g tunnels, galleries, dri s, etc. are called tunnelling. Drilling and blasting are a widely usedThe Lefa gold mine rock blasting process involves transforming the physical properties of the rock. During blasting, pollutants were released into the atmosphere and were often transported to houses by the wind. When the rocks explodes, noise, dust, and soil vibrations were generated which can affect the community and wildlife. This Characterization of the rock blasting process impacts in
احصل على السعر
(PDF) Possible ways of optimizing blasting operations
Blasting is one method of mining solid rock masses. The operation parameters, i.e. burden, blast hole and row spacing, stemming length, subdrilling length or explosive charge mass per single delayThe particle emissions are mainly generated during the material handling and combustion process of the equipment (CO, CO 2, SO X, NO X and PM10). Comparing the particle emissions for both extraction methods, the main difference between mechanical extraction and blasting will mainly be in the primary extraction and load and haul processes.LCA analysis and comparison in quarrying: Drill and blast vs
احصل على السعر