
Size reduction control in cone crushers ScienceDirect
There are two main cone crusher types (Hydrocone crusher and Symons crusher), of which only the Hydrocone crusher is capable of manipulating CSS during We review the state of the art developments in process modeling and cone crusher control from 1972 to 2020. • The steady-state model of Whiten (1972) is still used A review of modeling and control strategies for cone crushers
احصل على السعر
Geometric analysis of cone crusher liner shape
1. Introduction Even though the original cone crusher patents were accepted almost 100 years ago (in the mid 1920's by E B Symons), the cone crusher concept A cone crusher basically consists of a cone-shaped mantle describing a conical motion inside a cone-shaped bowl, see Fig. 1. As the mantle rotates, new rocks Modeling and Simulation of Cone Crushers ScienceDirect
احصل على السعر
Modelling of flow in cone crushers ScienceDirect
The possibility to simulate and predict cone crusher performance is of great interest for the development of crushers as well as for the design and optimization Inertia cone crushers are widely used in complex ore mineral processing. The two mass variables (fixed cone mass and moving cone mass) affect the dynamic performance of the inertia cone crusher.Influence of Two Mass Variables on Inertia Cone
احصل على السعر
Cone Crusher Spring Cone Crusher
Gyradisc Cone Crusher It was developed based on spring cone crusher. These two variants have the same main structure and operating principle, and they are mining industry. The cone crusher concept was developed in the early 20th century and the basic layout of the machine has not changed dramatically since then. CONE CRUSHER MODELLING AND SIMULATION
احصل على السعر
Minerals Free Full-Text Constant Wear Criterion
Cone crushers are high-efficiency particle crushing instruments utilized in a variety of industries [ 1 ]. The crushing chamber is one of the core components of a cone crusher [ 2 ], and is directly related Chamber sizes vary between three and six numbers within a particular designated crusher size to produce fine, medium or coarse sized product. The Standard cone crushers are Cone Crusher an overview ScienceDirect Topics
احصل على السعر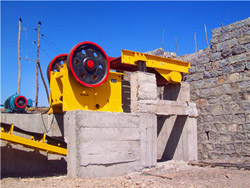
Cavity level's effect on cone crusher performance and production
Dusty jacobson • Peter janssen Victor urbinatti TON Corporation, USA Cavity level’s effect on cone crusher performance and production The effect of varying cavity level inside a high speed cone crusher chamber was abstract studied in relation to capacity, power utilisation, and reduction properties.Choke feeding a cone crusher, whereby a head of material is maintained in the chamber, provides rock-on-rock breakage (Evertsson, 2000). Jacobson and Janssen (2010) studied the effect of varying cavity level inside a high-speed cone crusher chamber in relation to capacity, power utilization, and size reduction properties. They concluded anDEM-based design of feed chute to improve performance of cone crushers
احصل على السعر
What are the different types of cone crushers? LinkedIn
It has the added benefit of low operating costs due to its ability to be adjusted for varying size ranges of feed. types of cone crushers. Symons cone crusher: This is a type of cone crusherTaking the PYGB1821 multi cylinder hydraulic cone crusher as an example, it is proved that the service life of the new liner is improved by more than 14.3%. Measurement of wear value of dynamicDesign of crusher liner based on time varying uncertainty
احصل على السعر
US20050269436A1 Cone rock crusher Google Patents
An improved cone-style rock crusher. The rock crusher may be adjusted for varying rock crushing specifications, including different speeds, throws, and liners. The rock crusher comprises a frame that supports a crushing bowl, a crusher head and a shaft, with the shaft being secured to the crusher head. A domed feed plate may be secured onto Semantic Scholar extracted view of "Cone crusher chamber optimization using multiple constraints" by Dong Gang et al. Skip to search form puts forward the time-dependent design method considering the load fluctuation factors for the liner based on the time-varying uncertainty theory. In this method, the time-varying Expand. 2. PDF. Save.Cone crusher chamber optimization using multiple constraints
احصل على السعر
Output prediction of cone crushers ScienceDirect
The outlet is a well defined boundary, but the inlet could be the origin for the derivation as well. Output prediction of cone crushers 219 Pivot point r (rpl, bpl ) Concave profile Mantle profile Li ----- (rp2, bp2) O, 03, n Open ~ Closed Neutral position Fig.3 Chamber geometry for a tentative cone crusher.Features. Nordberg® GP500S™ secondary cone crusher is engineered for economic and efficient size reduction in secondary crushing applications. It is often used in aggregates production and mining operations. The crusher’s heavy-duty design and use of high-quality components with optimized wear parts keep the operating costs down.Nordberg® GP500S™ secondary cone crusher TON
احصل على السعر
A review of modeling and control strategies for cone crushers
The minimum distance between the mantle and concave is defined as the closed side setting (CSS) of the cone crusher. The CSS is easily changed online in a large variety of commercial crushers; different principles of CSS adjustment are described in (Quist, 2017).The maximum distance between the mantle and concave, on the other geometry, crusher dynamics and rock material characteristics. Concave, mantle, eccentricity and location of the pivot point together form the chamber. resulting motion of the mantle and main shaft(PDF) Cone Crusher Performance ResearchGate
احصل على السعر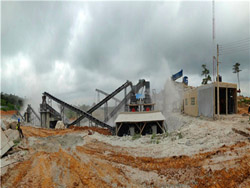
Feed-hopper level estimation and control in cone crushers
A common practice is to regulate the feed-hopper material level h in order to guarantee the choke-fed conditions. There are indications that higher feed-hopper level will result in smaller product size and higher throughput especially in a Symons crusher, and this property could possibly be used to control size reduction (Herbst and Oblad, 1985; The crushing chamber is the core component of a cone crusher, consisting of mantle and concave parts. Reducing the impact of crushing chamber wear on the performance of cone crushers and the Minerals Free Full-Text Constant Wear Criterion
احصل على السعر
Analysis of cone crusher performance with changes in
The fixed cone mass and moving cone mass of a balancing crusher are decreased by 78.9% and 22.8%, respectively, compared to without the balancing mechanism. View Show abstractThis research involves the optimization of aggregate production using the Taguchi approach to maximize the production rate of Gneiss stone. The L18 orthogonal array has been used to investigate how the CSS, throw, eccentric speed, and particle size affect the products of the cone of the crusher (its cumulative weight fraction). The CSS, Aggregate Production Optimization in a Stone-Crushing
احصل على السعر
Simulating a laboratory-scale cone crusher in DEM using
1. Introduction. Cone crushers are the most widely used type of crusher in the minerals and aggregate industries, given their robustness, ability to deal with rocks with a wide range of abrasiveness, good energy efficiency as well as good control of product size [1].Creating a new cone crusher design, selecting a crusher model from a particular GP100S™ crusher is an excellent choice whenever high reduction, first-class cubicity or great capacity is required. The optimized design of the Nordberg® GP100S™ castings makes it possible to use a higher power rating than any other cone crusher with an equal head diameter. Cavity designs provide maximum yields for required high-qualityNordberg® GP100S™ secondary cone crusher TON
احصل على السعر
Cone Crusher an overview ScienceDirect Topics
Cone crushers have gained such wide acceptance that they may be regarded as standard in the intermediate-range size-reducing machines. A schematic diagram of a cone crusher is shown in Fig. 4.6 A.The drive is similar to that of a gyratory crusher. The inner cone or ‘crushing head’ is supported by the tapered concentric spindle, which is rotated by the The throughput of a jaw crusher ranges between 30 and 1200 tph (Wills and Napier-Munn, 2015). Jaw crushers have been modelled previously; in 1953, Gauldie conducted a performance study of the jaw crusher, including a capacity model that handles varying speeds and closed side setting (CSS) (Gauldie, 1953).A fundamental model of an industrial-scale jaw crusher
احصل على السعر
Materials Free Full-Text Influence of Basalt Aggregate
After analyzing the grain size distribution and determining the shape and flakiness indexes, the basalt aggregate samples were crushed in the jaw crusher and the cone crusher. For the analysis of the crushing process, the original sample should be perceived as the aggregate sampled directly in its original state in the processing system.
احصل على السعر