
(PDF) Grinding in Ball Mills: Modeling and Process
A ball mill is a type of grinder widely utilized in the process of mechanochemical catalytic degradation. It consists of one or Ball-milling is a low-cost and green technology that offers mechanical actions (shear, friction, collision, and impact) to modify and reduce starch to nanoscale Ball-milling: A sustainable and green approach for starch
احصل على السعر
Ball milling: a green technology for the
These ball mills are the most widely used in the field of cellulose and they can be further divided into three groups: tumbler ball mills, vibratory mills The power consumption method was used to simulate the motor power and processing capacity of the Φ5.49 × 8.83 m ball mill. The results are presented in Fig. 4. Enhancing the capacity of large-scale ball mill through process
احصل على السعر
A process mineralogy approach to study the efficiency of
The primary ball mill operates in an open circuit (after the middle thickener) and the secondary ball mill operates in a closed circuit with a hydrocyclone.Abstract. A mineralogy, rheology, and energy consumption-based experimental characterization of chalcopyrite ball mill grinding processes, in both batch Experimental characterization of chalcopyrite ball mill
احصل على السعر
Modelling the performance of industrial ball mills using
Ball milling is an energy-intensive unit operation and usually consumes a major proportion of the power drawn by a typical mineral processing plant. Hence, The ball mill consumes about 25-30% of the total energy in the beneficiation plant, and hence any improvement will improve the overall economics of the plant. The power Performance optimization of an industrial ball mill for chromite processing
احصل على السعر
Mineral Processing Design and Operations ScienceDirect
The design of different types of Tubular Ball Mills used for size reduction of crushed Run-of-Mine ores is described in some detail followed by descriptions and mathematical considerations of their operation. Describes automation in mineral processing plants allowing maximum yields and consistent high concentrate grades; Outlines problemsQuantum Nanostructures (QDs): An Overview. D. Sumanth Kumar, H.M. Mahesh, in Synthesis of Inorganic Nanomaterials, 2018 3.6.1.1 Ball Milling. A ball mill is a type of grinder used to grind and blend bulk material into QDs/nanosize using different sized balls. The working principle is simple; impact and attrition size reduction take place as the ball Ball Mill an overview ScienceDirect Topics
احصل على السعر
Lithium Processing Plant, Equipment Mineral
1 天前lithium processing plant. 1. Lepidolite flotation plant. 1. Crushing & screening: The hopper + vibrating feeder automatically feeds the 0-500mm material into the jaw crusher. Jaw crushers are used to break large A cement mill is a fundamental component of the cement manufacturing process, playing a vital role in breaking down and grinding cement clinker into fine powder. This finely ground powder, when mixed with other materials, produces the building material we commonly know as cement. To achieve this crucial transformation, a cement mill What Are the Parts of a Cement Mills? Cement Ball Mill Production Process
احصل على السعر
(PDF) Rod Mill Product Control and Its Relation to
Main features of the laboratory tumbling rod mill. Experimental design of the rod mill experiments for modeling purposes. Vc is the critical rotational speed of the mill, the solid feed is 3 kgReason: This is a common problem mining ball mills face, resulting in low productivity and low ore processing efficiency. One reason may be the improper design of the grinding chamber, which affects the flow of materials and reduces grinding efficiency. Additionally, worn or damaged liners can hinder the grinding process by reducing the Inventory Of Common Faults And Solutions Of Mining Ball Mill
احصل على السعر
(PDF) Grinding in Ball Mills: Modeling and Process Control
A ball mill is a type of grinder widely utilized in the process of mechanochemical catalytic degradation. It consists of one or more rotating cylinders partially filled with grinding balls (madeCIL (Carbon In Leach) is the carbon leaching method for gold extraction. Normally the CIL process can concentrate gold from 2.5–3.5 g/t in ore to 2000 to 6000 g/t on carbon. CIL gold process is suitable for beneficiating oxidized gold ore with low sulfur and mud content. It is characterized by low cost, short infrastructure construction time and CIL Gold Mining Process, Equipment Mineral Processing
احصل على السعر
Ball Mill Ball Mills Wet & Dry Grinding DOVE
2 天之前DOVE small Ball Mills designed for laboratories ball milling process are supplied in 4 models, capacity range of (200g/h-1000 g/h). For small to large scale operations, DOVE Ball Mills are supplied in 17 models, capacity range of (0.3 TPH 80 TPH). With over 50 years experience in Grinding Mill Machine fabrication, DOVE Ball Mills asInapakurthi et al. (2020) used recurrent neural networks to model a grinding circuit in lead-zinc ore beneficiation process, consisting of a rod mill, ball mill, two hydro-cyclones and two water sumps (primary and secondary). The system consists of three MV (ore feed rate and water supply in the sumps) and three CV (throughput, % solids Control of a closed dry grinding circuit with ball mills using
احصل على السعر
4 Minerai proceshg simulation software Download Table
A multi-compartment tube ball mill in closed circuit with an air separator is very common for grinding of clinker product in most cement plants. Ardabil cement plant in north-west of Iran producesNowadays, ball mills are used widely in cement plants to grind clinker and gypsum to produce cement. In this work, the energy and exergy analyses of a cement ball mill (CBM) were performed andEnergy and exergy analyses for a cement ball mill of a
احصل على السعر
Performance optimization of an industrial ball mill for chromite processing
An increase of over 10% in mill throughput was achieved by removing the ball scats from a single -stage SAG mill. These scats are non- spherical ball fragments resulting from uneven wear of ballsHere we studied the relationship between the characteristics of the starting lignocellulosic plant material and the properties of the resulting ultrafine powder in different ball-mill process routes. Methods: Two lignocellulosic biomasses (pine bark and wheat straw) with contrasted compositional and mechanical properties were milled using Properties of biomass powders resulting from Open
احصل على السعر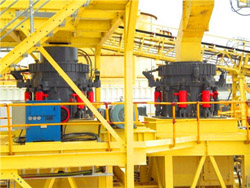
A specific energy-based size reduction model for batch grinding ball mill
A particle size reduction model has been developed as the first component of an upgraded ball mill model. The model is based on a specific energy-size reduction function, which calculates theAs you all know, the process of a cement manufacturing plant can be divided into several steps, including crushing, raw milling, clinker calcining, cement milling (or cement grinding), packing and etc. In the complete cement production line, the cement mill process plays a very important role. The design of cement milling and cement mill Ball Mill, Vertical Roller Mill AGICO Cement Plant
احصل على السعر
Modelling the performance of industrial ball mills using
Ball milling is an energy-intensive unit operation and usually consumes a major proportion of the power drawn by a typical mineral processing plant. Hence, substantial economic benefits can be achieved by optimal design and by operating ball milling circuits under optimum process conditions. This requires an accurate ball mill The underflow is sent to a secondary ball mill and trommel screen, for additional grinding and classification. Using froth flotation, the copper minerals separate from the gangue and rise to the froth layer of the flotation cell. In turn, the copper-rich bubbles are removed or transferred to the next stage of flotation for further processing.Copper Processing Multotec
احصل على السعر
(PDF) Controlling the Ground Particle Size and Ball Mill
The proposed method has been practically implemented on the ball mill of Lakan lead-zinc processing plant. Also, a prototype of the device was built. The test results show that the optimal load
احصل على السعر