
Review on vertical roller mill in cement industry & its
All grinding processes in the cement industry are operated dry. The capacities of grinding mills range from 300 − 1000 TPH for Limestone and for cement The modular vertical roller mill for grinding cement raw material, cement clinker, and additives with an installed power of up to 12,000 kW was specifically Grinding process optimization IEEE Xplore
احصل على السعر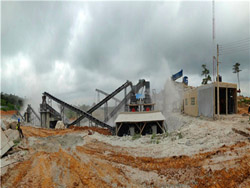
OK™ Raw and Cement Mill FLSmidth
Our vertical roller mill offers optimum raw, cement and slag grinding Our best-in-class OK™ Mill is a globally successful vertical roller mill solution for grinding raw material, cement Construction Solutions. Cement Industry. Cement production has increased more than thirty-fold since 1950 and almost four-fold since 1990.¹ Cement plants are expanding and in need of highly efficient processes more than Cement Industry Sika
احصل على السعر
The influences and selection of grinding chemicals in cement grinding
In addition, the bulk material becomes fluidized and that makes the transportation along the mill easier. Today, grinding chemicals are reported as capacity 1. Introduction For all dry grinding applications, cement production is certainly the most important. The estimate for the world energy consumption for cement Cement grinding optimisation ScienceDirect
احصل على السعر
Energy-Efficient Technologies in Cement Grinding
In this chapter an introduction of widely applied energy-efficient grinding technologies in cement grinding and description of the operating principles of the related equipments and comparisons over Product Description Cement ball mill is mainly used as the finished products and raw materials grinding equipment in cement plant, which can meet the superfine grindingChina Cement Mill, Cement Mill Manufacturers, Suppliers,
احصل على السعر
The growing cement industry of the UAE Global Cement
The plant has four clinker kilns and six cement grinding mills: Kilns 1&2: 750t/day each; Kiln 3: 2000t/day; Kiln 4: 10,000t/day; 2x cement ball mills: 2x40t/hr; 2x cement ball mills: 2x45t/hr; 2x cement vertical roller mills: 2x210t/hr. UCC is the UAE's only oil well cement producer. It produces the Norwell brand API 10 A Class G (HSR) oilChina Cement Mill manufacturers Select 2023 high quality Cement Mill products in best price from certified Chinese Mill, Grinding Equipment suppliers, wholesalers and factory on Made-in-China. Construction, Machinery, Chemical, Petroleum, Grind, Refractory Material; ProcessingChina Cement Mill, Cement Mill Manufacturers, Suppliers,
احصل على السعر
Energy-Efficient Technologies in Cement Grinding
The energy consumption of the total grinding plant can be reduced by 20–30 % for cement clinker and 30–40 % for other raw materials. The overall grinding circuit efficiency and stability are A molecular modified PCE-type GA was self-synthesized, and the grindability concerning grinding duration and particle size distribution of ground cement was evaluated. Setting time, flowability, hydration heat, mechanical properties and microstructure of the ground cement were also investigated. The results show that: PCE-type GA is Effects of Polycarboxylate-based Grinding Aid on the
احصل على السعر
Cement Grinding Plant Overview Cement Grinding Unit AGICO Cement
The cement roller press and cement mill are used to grind the cement raw material to the required particle size and packaging. There are two types of cement mill including a ball mill and vertical cement mill. The above is only a summary of the ideas formed in the survey of the construction of the grinding plant by AGICO Cement. In factIn the past, high pressure grinding rolls (HPGR), vertical roller mills (VRM) had positive effects on the overall energy utilization of cement grinding however some quality issues had also beenCements ground in the vertical roller mill fulfil the quality
احصل على السعر
The Decision Algorithm of Cement Mill Operation Index
The cement grinding system consists of a coarse grinding system mainly by roller press and a fine grinding system by ball mill, the energy flow in the grinding process moves along the material and gas paths, as shown in Fig. 2, which shows the equipment composition and production diagram of the cement grinding system, where the solid line Cement grinding unit cost. Take the annual output of 600,000 tons of large-scale cement grinding station as an example, there are three common options can be recommended: SCHEME 1: roller press + φ 3.2 ×13m ball mill; SCHEME 2: φ 3.8 ×13m closed mill; SCHEME 3: clinker fine crusher + cement roller press+φ 3.2 ×13m ball mill.Cement Grinding Unit Cement Grinding Plant Cement Grinding
احصل على السعر
Characterization of various cement grinding aids and their
The evaluation of the grinding aids (GA) was carried out by interground 0.015% of each grinding aid with gypsum and a Portland cement clinker (95% clinker, 5% gypsum), in a 1 kg laboratory rotating ball mill, using steel balls as grinding medium, to a Blaine surface area of about 4000 cm 2 /g (according to the Blaine air permeability Mill Feed Sep. Return Final Product System Fan Figure 1: Closed circuit grinding system. milling system is a delicate task due to the multivari-able character of the process, the elevated degree of load disturbances, the different cement types ground in the same mill, as well as the incomplete or missing information about some key process charac-OPTIMIZING THE CONTROL SYSTEM OF CEMENT
احصل على السعر
Cement Mill Cement Grinding Machine AGICO
Coal mill is the main equipment in the pulverized coal preparation process.Because calcining top-grade cement clinker requires a stable supply of coal powder as the fuel of cement kiln, and more than 85% of AGICO Cement is a cement equipment manufacturer with more than 20 years’ experience. We are the long-term partner of many large and medium-sized cement enterprises in different countries, providing cement Ball Mill In Cement Plant Cement Ball Mill
احصل على السعر
Grinding process optimization IEEE Xplore
As a world-wide leader in grinding solutions for the cement industry and understanding the changing needs of cement producers and how to tailor solutions to meet those needs. Optimizing output, improving efficiency, and reducing CO2 emissions while keeping investment costs to a minimum are common challenges that the modular vertical The cement industry is responsible for approximately 7% of anthropogenic CO 2 equivalent (CO 2e) emissions 1,2 with the highest carbon intensity of any industry per unit of revenue 3.To combatTowards a business case for CO2 mineralisation in the cement
احصل على السعر
Minerals Free Full-Text Analysis and Optimization of Grinding
This work concentrates on the energy consumption and grinding energy efficiency of a laboratory vertical roller mill (VRM) under various operating parameters. For design of experiments (DOE), the response surface method (RSM) was employed with the VRM experiments to systematically investigate the influence of operating parameters on The cement clinker grinding circuit reduces the feed from 80% passing size between 10 and 20 mm to 100% passing 90 μm.The size reduction takes place in a two- compartment tube mill; the first compartment of the mill Cement grinding optimisation ScienceDirect
احصل على السعر
Loesche Mills for Cement and Granulated Blast Furnace
Grinding of cement clinker and granulated blast furnace slag in roller grinding mills (vertical airswept grinding mills) is a technology introduced by Loesche. The first use of a Loesche mill, with a grinding track diameter of only 1.1 metres, was used as long ago as 1935. However, the breakthrough in grinding this type of material on the vertical[Show full abstract] performances of these cement grinding technologies, industrial scale data were collected from HPGR-ball mill, VRM, Horomill and multi-chamber ball mill closed circuits.The(PDF) Pregrinding technology ResearchGate
احصل على السعر
Cement Grinding Plant Price, 2023 Cement Grinding Plant Price
Cement Grinding Plant Price Select 2023 high quality Cement Grinding Plant Price products in best price from certified Chinese Cement Production Plant manufacturers, Cement Mixing Plant suppliers, wholesalers and factory on Made-in-China Construction, Cement Production; Certification : CE, ISO; Customized Industry Mining There are four stages in the manufacture of portland cement: (1) crushing and grinding the raw materials, (2) blending the materials in the correct proportions, (3) burning the prepared mix in a kiln, and (4) grinding the burned product, known as “ clinker ,” together with some 5 percent of gypsum (to control the time of set of the cement).Cement Extraction, Processing, Manufacturing Britannica
احصل على السعر