
Grinding process within vertical roller mills: experiment and
Based on screening analysis, laser size analysis, grindability and rigidity tests of samples collected on line from a cement and a power plant, a simulation of the grinding process in vertical roller mills was carried out. The simulation calculation used a In this article, the critical enabling roller grinding technology is introduced toward higher stability, efficiency, accuracy, and Advances in grinding technology in China with
احصل على السعر
Grinding process optimization IEEE Xplore
Grinding process optimization — Featuring case studies and operating results of the modular vertical roller mill Abstract: As a world-wide leader in grinding DOI: 10.1016/S1674-5264(09)60018-1 Corpus ID: 110668154; Grinding process within vertical roller mills: experiment and simulation @article{Wang2009GrindingPW, [PDF] Grinding process within vertical roller mills: experiment
احصل على السعر
A cement Vertical Roller Mill modeling based on the
In the grinding process of a VRM, three types of forces are assigned: compression, shear, and centrifugal, with compression forces attributed to breakage The crushing process in the vertical roller mill (VRM) has been systematically investigated via DEM. Significant effects of material properties and Analysis of vertical roller mill performance with changes in
احصل على السعر
Indicate Contributions from Several Radial
increasing output, lowering breakdowns and optimizing the grinding process which eats almost 60% of power cost. In recent years vertical roller mill (VRM) has proved to be a A model of the capture of material by corrugated rollers in a crusher is described. A formula is proposed for the wrapper dimensions and the angular distance Modeling and Industrial Development of Grinding Processes in Roller
احصل على السعر
Analysis and Optimization of Grinding
This work concentrates on the energy consumption and grinding energy efficiency of a laboratory vertical roller mill (VRM) under various operating parameters. For design of experiments (DOE), the Abstract. Based on screening analysis, laser size analysis, grindability and rigidity tests of samples collected on line from a cement and a power plant, a simulation Grinding process within vertical roller mills: experiment and
احصل على السعر
The mechanism investigation of ultrasonic roller dressing
To clarify the ultrasonic roller dressing mechanism of the vitrified bonded cubic boron nitride grinding wheel (V-CBN), the collision number model between the diamond dresser and CBN grits was established based on the geometric and kinematics analysis. The influence of each dressing parameter on the collision number was 2 Vibration signal acquisition for roller grinding The grinder used in the test is the MK9025A CNC optical curve grinder from Shanghai No. 3 Machine Tool Factory. Use diamond grinding wheels to dress the diamond rollers. The bonding agent of the grinding wheel is ceramic, the particle size is 140/170, the width is 3mm, and the diameter is 200mm.Analysis of vibration signal of diamond roller grinding
احصل على السعر
Method for graphically evaluating the workpiece s
γ is the radius of roller. In the grinding process, the grinding wheel generates workpiece’s contour. Referring to Fig. 3, the grinding point P, roller’s center O r, and grinding wheel’s center O lie on a straight line whose normal angle is θ k. R is the radius of grinding wheel. X k and C k are the position of translational and1 天前The grinding experiments of the PRSM nut samples in Section 2.1 were performed using the CNC internal thread grinding machine (SK7605, produced by Hanjiang Machine Tool Co., Ltd., China), as shown in Fig. 5.The grinding machine belongs to a four-axis numerically controlled machine tool, which uses the German Siemens 828D numerical A study of precision grinding of micro-pitch internal thread
احصل على السعر
Energy-Efficient Technologies in Cement Grinding IntechOpen
The energy consumption of the total grinding plant can be reduced by 20–30 % for cement clinker and 30–40 % for other raw materials. The overall grinding circuit efficiency and stability are improved. The maintenance cost of the ball mill is reduced as the lifetime of grinding media and partition grates is extended. 2.5.Machining 101: What is Grinding? Grinding takes an abrasive — often attached to a wheel — and uses its many grains to cut a workpiece. Variations on this process are useful for a wide variety of applications. #Basics. Evan Doran. Associate Editor, Modern Machine Shop. On its surface, grinding seems simple: a machine takes a Machining 101: What is Grinding? Modern Machine Shop
احصل على السعر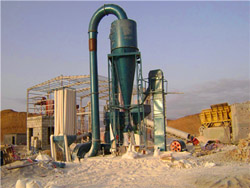
(PDF) Analysis of vibration signal of diamond roller grinding
Abstract. According to the non-linear and non-stationary characteristics of the vibration signal in the roller grinding manufacturing process, the background signals, namely the vibration signalBased on the above research on the mechanical data system and the characteristics of the grinding process, this paper presents the research architecture of intelligent grinding process driven by data into five layers (as shown in Fig. 1): data acquisition layer, data processing and fusion layer, data mining and analysis layer, data Intelligent technology in grinding process driven by data: A
احصل على السعر
Mechanics of self-rotating double-disc grinding process
Abstract and Figures. Unlike most double-disc grinding processes, which use forced workpiece rotation, some double-disc processes rely on workpiece self-rotation driven by non-uniform shear forcesA study conducted by Gerold et al. (2012) showed that VRM was able to grind copper and slag with the energy saving of 22.9% and 34.4% respectively compared to conventional grinding circuits. Wear rate is another criterion that is needed to be considered. In this context, Erkan et al. (2012) in their study compared the wear rates of rod-ballCopper ore grinding in a mobile vertical roller mill pilot plant
احصل على السعر
(PDF) A comprehensive review on the grinding
A comprehensive review on the grinding process: Advancements, applications and challenges. ARCHIVE Proceedings of the Institution of Mechanical Engineers Part C Journal of Mechanical The crushing process in a four-roller system includes two stages: preliminary crushing by the upper rollers; and final crushing by the lower rollers A.P., Vlasenko, D.A., and Levchenko, E.P., Study and substantiation of design and technological parameters of the grinding process for sintering fluxes in hammer mill, Chern. Met., 2019, Modeling and Industrial Development of Grinding Processes in Roller
احصل على السعر
Optimization of Cylindrical Grinding Process Parameters
Grinding Process Parameters on oEn15AM Steel Grinding process is surface finishing process generally used to smoothen the surfaces by removing the limited quantity of material from the already machined surfaces. Cylindrical grinding or abrasive machining is the most popular machining process of removing metal from a workThus, unsurprisingly, the grinding process is the object of extensive research of the past 20 years, especially by modelling and simulation. For grinding processes, there exist various types of simulation based on either the analytical theory [1], or the empirical models of the process [2]. The focus of this two-part paper, however, is theSimulation of precision grinding process, part 1: generation
احصل على السعر
Development of a hybrid particle swarm optimization
In the field of metal rolling, the quality of steel roller’s surface is significant for the final rolling products, e.g., metal sheets or foils. The surface roughness of steel rollers must fall into a stringent range to guarantee the proper rolling force between the sheet and the roller. To achieve the surface roughness requirement, multiple grinding passes have High-speed grinding process parametersHSG is characterised by efforts to improve the economics of the process by increasing material removal rates and simultaneous improvements of process stability, capability and machining quality. In this way, an increased cutting speed is a prerequisite for increased productivity.High-performance grinding—A review ScienceDirect
احصل على السعر
Analysis of vertical roller mill performance with changes in
A specially designed laboratory-scale VRM was constructed in the powder research center in Hefei, China. Fig. 1 represents the schematic diagram of VRM utilized in the experiment and DEM simulations. The diameter of the millstone and grinding roller are 600 mm and 340 mm respectively, and the angle between the centerline of the grinding With the introduction of the high compression machines such as High Pressure Grinding Rolls (HPGR), Vertical Roller Mills (VRM) and Horomills, efficiency of the grinding circuits was improved in terms of energy and downstream effects. Among these devices, vertical roller mills have an important position in cement and mining industry.Operational parameters affecting the vertical roller mill
احصل على السعر
JMMP Free Full-Text Optimization of Wet Grinding
Guided by the results obtained above, we used the large wet-grinding machine to grind large steel sheets. The size of the workpiece was 1219 mm × 2438 mm × 8 mm. The grinding conditions were changed to a spindle speed of 150 rpm, a surface pressure of 0.2 MPa, and a lateral speed of 15.4 mm/s.A cement Vertical Roller Mill modeling based on the number of breakages. Vertical roller mills (VRM) are widely used to grind, dry, and select powders from various materials in the cement, electric power, metallurgical, chemical, and nonmetallic ore industries. For the sectors above, the VRM is a powerful and energy-intensive grinding Operational parameters affecting the vertical roller mill
احصل على السعر