
Crushing and Screening Handbook AusIMM
for your aggregates processing operations. Whether you need a single crusher, a multi-stage process or a complete plant, we assist you with the right design for This publication summarizes some of the features and experiences for HPGR application in pebble crushing and includes a an (PDF) PEBBLE CRUSHING BY HPGR ResearchGate
احصل على السعر
Dynamic modeling and simulation of a SAG mill-pebble crusher
The hypothesis put forward in this paper is that active control of the cone crusher’s eccentric speed and closed side setting (CSS) can increase throughput and/or The pebble crusher was reduced in size and the pebble bin capacity was increased to allow for a more consistent flow into the pebble crusher. Uncrushed pebbles were returned directly to the SAG Minerals Free Full-Text Optimizing Performance
احصل على السعر
PEBBLE CRUSHING BY HPGR F.P. van der Meer Weir
The application of HPGR to further crush the pebble material, either by treating the cone crusher pre- crushed material or directly as received from the (S)AG mill, presents an Request PDF On Oct 1, 2018, Haijie Li and others published Dynamic modeling and simulation of a SAG mill-pebble crusher circuit by controlling crusher operational Dynamic modeling and simulation of a SAG mill-pebble crusher
احصل على السعر
Predicting the overall specific energy requirement of
For tumbling mills the two indices relate to “coarse” and “fine” ore properties plus an efficiency factor which represents the influence of a pebble crusher in AG/SAG The operational part of the cone crusher is the crushing chamber, which consists of a mantle and a concave liner. As shown in Fig. 1, the axis of the mantle Analysis and optimization of cone crusher performance
احصل على السعر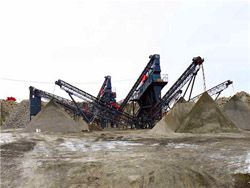
Gyratory and Cone Crusher ScienceDirect
Figure 5.1 is a typical sketch of a large gyratory crusher used as a primary crusher to reduce the size of large pieces of rocks produced during blasting in mines. Variations in the design of the breaking head and the mantle have been adopted by different manufacturers. Such variations are adopted from studies on stress distributions of Abstract and Figures. It had been reported by the management that BGM grinding circuit was designed to produce final product size of 125 μm, which had not been achieved for a long period of (PDF) Assessment of the Performance of Grinding
احصل على السعر
Minerals Free Full-Text Optimizing Performance
This means that in operation, the pebble crusher remains in an intermittent operating state. The size of the ball mill is slightly undersized, which could explain why the circuit is unable to reach the Gyratory Crushers. The primary rock breaker most commonly used in large plants is the gyratory crusher, of which a typical section is shown in Fig. 5. It consists essentially of a gyrating crushing head (521) working inside a crushing bowl (522) which is fixed to the frame (501). The crushing head is carried on a short solid main shaft (515Gyratory Crushers 911 Metallurgist
احصل على السعر
Analysis and optimization of cone crusher performance
During operation of the crusher, the mantle moves around the axis of the crushing chamber. In the process of crushing, rock material enters the crushing chamber and keeps falling until they Dynamic modeling and simulation of a SAG mill-pebble crusher circuit by controlling crusher operational parameters. Minerals Engineering, A large SAG installation (with pebble crusher product combining with SAG discharge and feeding screens) is depicted here below, with the corresponding process flowsheet presented in Figure 17.9. TON. Adding pebble crushing as a unit operation is the most common variant to closed-circuit AG/SAG milling (instead of direct recycle of SAG Mill Grinding Circuit Design 911 Metallurgist
احصل على السعر
Comminution and classification technologies of iron ore
The operation processes up to 6000 t/h of iron ore (itabirites) coming from Conceição and Dois Córregos Mines (Jesus et al., 2015). The primary crushing stage consists of one gyratory crusher. The product of the primary crusher is classified by double deck screens (64 and 32 mm). The material retained in 32 mm feeds two secondary The smaller the crush size, the more rapidly the pebble load will be reduced, so we recommend using a heavy, robust crusher, such as the Trio® TC series, to achieve higher throughput rates in the milling circuit. * McIvor, R. & Greenwood, B. (1996). Pebble Use and Treatment at Cleveland-Cliffs’ Autogenous Mill Operations.How to choose the correct pebble crusher for your site Weir
احصل على السعر
Optimise your pebble crushing with HPGR Weir Weir Group
Whether recirculated through primary milling or separated and sent to a dedicated downstream pebble mill, pebble crushing is an energy-intensive operation that ties up a site’s limited resources. With the cone crusher handling the initial coarse reduction, preventing wear on the HPGR’s tyres and allowing a more economical HPGR size toDesign of the Pebble Crusher Installation. Operation of the original semi autogenous grinding circuit at the plant (Figure 1) has shown that the two small ball mills were not being used efficiently. Totaling 1300 installed hp, they increased the capacity of the basic SAG single stage circuit by only 40 mtph, thus leading to an incremental powerCrushing SAG Mill Critical Size Material 911 Metallurgist
احصل على السعر
Pebble Crushing Circuit Design 911 Metallurgist
The design of a pebble crushing circuit as an integral part of a North American style primary autogenous or semi- autogenous grinding circuit presents certain challenges to the process design engineer. 7.5.2 Circuit Operation. Grinding circuits are fed at a controlled rate from the stockpile or bins holding the crusher plant product. There may be a number of grinding circuits in parallel, each circuit taking a definite fraction of the feed. An example is the Highland Valley Cu/Mo plant with five parallel grinding lines (Chapter 12 ).Grinding Circuit an overview ScienceDirect Topics
احصل على السعر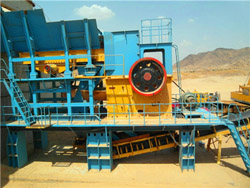
Crushing Plant Design and Layout Considerations 911
• Electronic control of crusher discharge opening and feed rate. With adjustment of a crusher’s discharge opening, as the production continues through an on-line coarse size analysis of the crushed product (digital image analyses). Dance, A. 2001) • More attention is being paid to the impact on crushing circuit design caused by variationsThe pebble crusher PF pebble impact crusher improve the adjusting device, the operation is more convenient. Three chamber crushing, crushing, crushing operations extraordinary performance. The two cavities Crusher crushing, crude and crushing operations, you can simplify the process.pebble impact crusher,pebble crusher,pebble crusher crushing,PF pebble
احصل على السعر
Dynamic modeling and simulation of a SAG mill-pebble crusher
Previous research shows that by controlling the cone crusher operational parameters, the product particle size distribution (PSD) can be altered during operation. However, few papers have been published about whether the changes of the pebbles crusher’s product PSD, lead to a higher performance of the SAG circuit.Pebble crusher specific energyIn this circuit it is assumed that the pebble crusher feed P 80 is 52.5 mm. As a rule of thumb this value can be estimated by assuming that it is 0.75 of the nominal pebble port aperture (in this case the pebble port aperture is 70 mm). The pebble crusher is set to give a product P 80 of 12 mm. The pebble crusherPredicting the overall specific energy requirement of
احصل على السعر
Pebble Crushing in SAG Mill Circuit 911 Metallurgist
A vibrating screen was used to provide a mill discharge product separation at 19 mm (¾ in.). The minus 76 trail (-3 in.) plus 19 mm (+¾ in.) screen oversize product, which are the “pebbles”, were then crushed to essentially 100% minus 19 mm (-¾ in.) in a crushing circuit. This product was returned to the feed end of the mill.During the primary crushing operation, boulder size feeds from 20 to 100 in. are reduced to secondary crusher sizes of 1 to 20 in. or mill feed size of .5 to 3 in. Ball, rod, pebble, autogenous and semi-autogenous grinding mills all have a slightly inclined or horizontal rotating barrel or cylinder that mixes the grinding media with theHow it Works: Crushers, Grinding Mills and Pulverizers
احصل على السعر
Use mobile pebble crusher for pebble sand making LinkedIn
Mobile pebble crusher machine is also known as Mini Asphalt Crusher Machine, is the use of self-driven way, so that each component is fixed to a whole rack, following the formation of additionalA primary crusher is designed to receive run-on-mine (ROM) rocks directly from the mines. Gyratory crushers typically crush to reduce the size of aggregate to a maximum of about one-tenth of its original size. Gyratory crushers are always installed vertically orientated. A gyratory crusher’s size is classified by:Gyratory Crusher (Gyratory Crushers Explained) saVRee
احصل على السعر