
Clean Air Flow Test of a Pulverizer ResearchGate
The purpose of the “clean air flow test of a pulverizer” is to achieve design rate of primary air flow through each pulverizer at any time and to ensure equal flow through each coal-airThe first step in optimizing combustion system performance is balancing the air and fuel flowing through each of the Pulverized Coal Pipe Testing and Balancing
احصل على السعر
sbm/sbm coal mill clean and dirty air test.md at main
Contribute to changjiangsx/sbm development by creating an account on .Precise Control & Measurement of Air and Coal < 0.5% air flow measurement < 1.0% coal flow measurement 10-120 ft/sec in-pipe Velocity 1400-5600 Pulverized Coal Extractive Testing Methods Airflow
احصل على السعر
CFD Analysis of Coal/Air Flow in Power Plants for
Sunith Bawankule M.Tech. student, Govt. College of Engineering, Amravati [M.S.], India Abstract: Unbalanced coal/air flow in the pipe systems of coal-fired power 1. Combustion tuning of a pulverized coal boiler begins with balancing the air and fuel flows in the coal pipes from the pulverizers to the burners. Note that each of the coal pipes is a...Pulverizers 101: Part III POWER Magazine
احصل على السعر
Soft sensor for coal mill primary air flow based on LSSVR
Soft sensor for coal mill primary air flow based on LSSVR Abstract: In the power plant coal-fired units, the primary air for boiler combustion and coal powder Observer-Based and Regression Model-Based Detection of Emerging Faults in Coal Mills. Peter Fogh Odgaard, Sten Bay Jørgensen, in Fault Detection, Supervision and Safety Coal Mill an overview ScienceDirect Topics
احصل على السعر
[PDF] REAL TIME PULVERISED COAL FLOW SOFT SENSOR
For the steady state coal mill model development, plant measurements such as airflow rate, differential pressure across mill etc., are considered as inputs/outputs. The mathematical The improved ignition of coal/air flow was at a distance of 0.8-1.4 m to the burner outlet with increased Rbsa/Rsa ratio. Compared with the boiler before retrofit, under Rbsa/Rsa ratios of 47.1/13.5 and 51.5/9.3, the flue gas temp. in the primary combustion zone of the retrofitted boiler increased slightly.A Control Strategy of the Air Flow Rate of Coal-Fired Utility
احصل على السعر
World’s First Coal to Biomass Conversion Using
The BT-220W surfactant is the same wetting agent used at Thunder Bay GS for operation on coal. The Walker Wetting test results indicate a significant improvement should be realised when usingcoal mill A and coal mill C; 3. 120 MW load, comparative test for the start and stop of the combustion optimization system under combined operation of coal mill A and coal mill B. 4. Reference Performance test code for utility boiler GB10184-1988. 5. Measuring Point, Method and Instrumentation 5.1 Flue Temperature MeasurementMinhang Power Plant, Shanghai Electric Power Co., Ltd.
احصل على السعر
CFD Analysis of Coal/Air Flow in Power Plants for
By carrying out general clean air flow test, orifice flow restrictor is fitted in the system. Air flow test is carried out by passing primary air from these system and velocity is measured at the outlet in furnace. The velocity at outlet is different for system due to the difference in length and numbers of bends.Our experience with both RP and MPS pulverizers has been that mills designed for a throughput of about 120,000 pounds of coal per hour, an HGI of about 45 to 50, and coal fineness exceeding 75%Pulverizers 101: Part I POWER Magazine
احصل على السعر
Microwave Measurement Can Optimize Coal-Fired Boiler Combustion
In many plants they may also know the amount of coal being fed to an individual coal mill, either by calibrating the feeder or using load cells on the feed. Clarion Energy Content Directors 10.1.The phenomenon was precisely the opposite of the level of 2019. However, we can note that the months of 2019 with a slightly higher level of dust concentration in the stack of the cement mill were August, with 4.6 mg/Nm 3, October, with 5.06 mg/Nm 3, and November, with 4.54 mg/Nm 3.Dust Emission Monitoring in Cement Plant Mills: A Case
احصل على السعر
Advancing flue-gas flow monitoring techniques Control
Efficient operation of today’s power plant largely depends upon accurate and repeatable measurement of primary and secondary airflow to coal mills, flue gas recirculation flow, overfire airflow, airflow to individual burners and other areas. Selecting the right flowmeter for flue gas or stack gas emission flow rate measurement is critical.Acceptable standards for best low-NO x burner performance are coal fineness of 75% passing a 200-mesh sieve and less than 0.1% remaining on a 50-mesh sieve. Fuel balance should be within the rangeCoal Pulverizer Maintenance Improves Boiler Combustion
احصل على السعر
4 Coal Mining and Processing The National Academies Press
The U.S. coal industry serves a vital role in the nation’s economy by producing fuel for more than half of its electricity. Despite the industry’s importance, industry financial data for 2005—the strongest year for the coal industry in recent years—shows that it is a relatively small industry with revenues totaling $20 billion to $25 billion and net income between $1 coal翻译:煤。了解更多。 英语-中文(简体) Chinese (Simplified)–English 英语-中文(繁体) Chinese (Traditional)–English 英语-荷兰语 荷兰语-英语 英语-法语 法语-英语 英语-德语 德语-英语 英语-印尼语 印尼语-英语 英语-意大利语 意大利语-英语 英语-日语 日语-英语coal中文(简体)翻译:剑桥词典 Cambridge Dictionary
احصل على السعر
How a little lab helps 'clean' coal firms win big
Filed Dec. 4, 2018, 2 p.m. GMT. “Clean” coal is a rich vein for American investors to mine, thanks to a lucrative subsidy offered by the U.S. government. For many producers of the fuel, theIf the PA flow is 20 to 40% higher than design, the PA/coal stream can outrun the SE air creating poor combustion at the burner. The coal and air generally do react, but higher up in the furnaceUnderstanding the Business of Coal Primary Air
احصل على السعر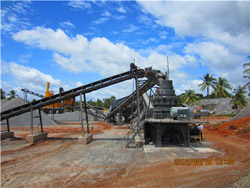
Successful Torrefied Biomass Test Burn at a Coal Power Plant
As we worked through trying to find a balance of primary air flow and mill temperature, the pressure drop across the mills slowly increased, even when the fuel flow was reduced to 30,000 lbm/hr.When using higher-chlorine coal, the FGD blowdown rate must be increased from approximately 100 gpm (using coal with 0.1% to 0.2% chlorine) to 200–300 gpm while using higher-chlorine coal. TheOperational Considerations When Burning Higher-Chlorine Coal
احصل على السعر
Managing air to improve combustion efficiency POWER
A best practice is to ensure that combustion is completed in the furnace with a stoichiometry of 1.15 to 1.20 (excess air of 15% to 20%) before the products of combustion reach the superheater. 3Adding additional heat transfer surface to the boiler will allow further reduction of the coal moisture content, with a projected 4.5% heat rate improvement and a more than 4.6% reduction of CO 2Improve Plant Efficiency and Reduce CO2 Emissions When
احصل على السعر
2016 Madhya Pradesh
• Efficiency test of each unit. • Performance test with special purpose instruments viz. clean air and dirty air flow test. • Condenser performance test. • APH performance test. • HP Heaters’ performance test. • Fire fighting mock drill. Overhaul related following actions to be taken from Operation Management perspective -The coal pulverizers are the heart of a pulverized coal–fueled boiler. About 75% of the opportunities for improvements in tuning are with the coal mills, primary airflow, and fuel line balancing.Typical Causes of Slagging and Fouling Problems in Boilers
احصل على السعر
Soft sensor for coal mill primary air flow based on LSSVR
In the power plant coal-fired units, the primary air for boiler combustion and coal powder conveying is directly related to the actual combustion chamber conditions. Therefore, the appropriate primary air flow is very important for the normal operations of the coal mill and even the whole units. Coal mill primary air flow soft sensor model was
احصل على السعر