
Gravity Concentration In Modern Mineral Processing
A review is presented of the range and type of gravity separation processes available and employed in modern ore treatment plants. Recent trends in gravity plant design, equipment and practices are identified to maximize productivity, improve metallurgical...A number of physical separation techniques for nickel (Ni) laterites have been investigated at laboratory and pilot plant scale and reported in the open literature. Preconcentration strategies in the processing of nickel
احصل على السعر
Pre-concentration of nickel in laterite ores using physical separation
This paper examines the effects of different physical methods on pre-concentration of nickel in laterite ores. The effect of ore mineralogy on choosing the best Tackling the problem of beneficiation of low-grade Ni laterites, the fundamentals of a novel chemo-physical concentration approach were presented in this Chemo-physical concentration of a Low-grade nickel laterite ore
احصل على السعر
Preconcentration strategies in the processing of nickel
Rao et al. (1995) investigated the preconcentration of Ni values from the lateritic chromite ore overburden from Sukinda, Orissa, India. The Ni values were hosted Abstract. A number of physical separation techniques for nickel (Ni) laterites have been investigated at laboratory and pilot plant scale and reported in the open Preconcentration strategies in the processing of nickel
احصل على السعر
Minerals Special Issue : Gravity Concentration MDPI
Gravity concentration can be defined as the process by which particles of different sizes, shapes, and densities are separated from each other by the force of Development of the gravity concentration flowsheet is discussed and the paper finishes with the description of two plants, one treating iron ore and the other cassiterite, as an indication of the diversity of gravity Gravity Concentration Methods SpringerLink
احصل على السعر
Chemo-physical concentration of a Low-grade nickel laterite ore
Tackling the problem of beneficiation of low-grade Ni laterites, the fundamentals of a novel chemo-physical concentration approach were presented in this PDF A number of physical separation techniques for nickel (Ni) laterites have been investigated at laboratory and pilot plant scale and reported in Find, read Preconcentration strategies in the processing of nickel
احصل على السعر
Gravity Concentration Methods SpringerLink
Development of the gravity concentration flowsheet is discussed and the paper finishes with the description of two plants, one treating iron ore and the other cassiterite, as an indication of the diversity of gravity nickel ore is the highest dehydroxylation process compared to other lateritic nickel ore types. It occurs at temperatures of 261270°C, while the removal of the hydroxyl group in the limonite nickel ore occurs at a temperature of 400600°C.12) The removal of hydroxyl groups in chlorite (Fe,Mg,Al) 3-(Si,Al) 2O 5(OH) 4 starts at 602°C andSelective Reduction of Laterite Nickel Ore J-STAGE
احصل على السعر
Preconcentration strategies in the processing of nickel
All Australian laterite operations crush the ore then reject particles greater than 1 mm to 2 mm, and the target nickel recovery in these processes is typically 70% (David 2008;Nice 2004;Quast etTo acquire understanding of Ni enrichment from laterite ore, the mineralogy and crystal chemistry of a low grade limonite type nickel laterite ore sample assaying 0.97% Ni from Indonesia wereRelationship between process mineralogical characterization
احصل على السعر
Minerals Free Full-Text The Geological Occurrence MDPI
Regarding gravity concentration, At the Talnakh Plant, processing of the sulphide ores is carried out using differential flotation, and the tailings represent only about 25–30% of the feed solids. The main difference in this processing technology is that the low nickel grade ore is a separate product,This paper examines the effects of different physical methods on pre-concentration of nickel in laterite ores. The effect of ore mineralogy on choosing the best strategy to upgrade nickel will be discussed. The findings of this project will help to unlock a substantial volume of nickel with significant value from laterite ores.Preconcentration strategies in the processing of nickel
احصل على السعر
(PDF) Process optimization of a chrome ore gravity concentration plant
Several techniques have been considered to treat slimes. Existing technologies for chrome concentration like spirals, shaking tables, magnets and flotation have been re-purposed to process chromeIn view of this, the maximum admissible Ni concentration established for agricultural soils on the basis of the 86/278/EEC directive of 30 mg kg −1 for acidic soils and 75 mg kg −1 for neutral alkaline soils seems to be protective for plants. Nickel is quickly taken up by plants from soils in the form Ni(H 2 O) 2+ 6 and, until toxicChromium and Nickel SpringerLink
احصل على السعر
Mineralogical Factors Affecting the Dense Medium Separation of Nickel
The sample of ore A showed a 54% total nickel upgrade from 0.43% in the ROM to 0.66% in the flotation feed, with an 87% nickel recovery to the flotation plant. Calculated results indicate that 44% of the ROM mass was rejected in the DMC overflow, which had a nickel grade of 0.13%.0.5, 1, 1.5 % solids A gravity force of 300 g, a solids% of 20%, a feed rate of 1 L/min, and water pressure of 0.5 psi were determined to be the optimum levels for achieving a minimum ash content of(PDF) Gravity separation by falcon concentrator
احصل على السعر
Spirals in Australia mineral processing Multotec
Minerals mined in Australia include iron ore, coal, gold, copper, nickel and zinc. Spiral concentrators are used in mineral processing for separating minerals. Multotec Australia has a range of gravity concentration The mineral phase transformation and migration of valuable metals for various laterite ores during calcination process was investigated, as well the influences of mineral phases and chemical compositions on magnetic properties, separation efficiency, and nickel contents in separated laterite ore. The results show that spinel nickel ferritePreconcentration strategies in the processing of nickel
احصل على السعر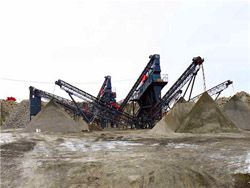
Table 1 . Chemical analysis of nickel ore reported as oxide
Analysis of the results revealed that 0.07% and 0.04% of the nickel were recovered from the tailing by Senfroth XP 516 and 200 respectively from the ores grade sample A, while 0.53% and 0.30% ofCopper-Nickel Ore Processing. Table of Contents. A nickel-copper sulphide concentrate was treated in a pilot plant at Warren Spring Laboratory during 1961, by a hydrometallurgical roast-leach-solvent extraction process devised to cleanly separate the metal values, and produce acid sulphate liquors containing the metals.Copper-Nickel Ore Processing 911 Metallurgist
احصل على السعر
Modeling and optimization of spiral concentrator for
In the present study, the tailings generated from a chromite ore beneficiary plant in India were investigated through a pyro-metallurgical route. The initial characterization confirmed the presence of nickel (0.5–0.9% Ni) in the ore, which led to the interest in smelting the ore to obtain nickel in the metal.Depletion in high-grade nickel sulfide ore, in contrast to the growing global consumption is making nickel-bearing laterite ores an attractive option for nickel production. Thus, upgrading nickel content by gravity concentration, before the hydro metallurgical or pyro metallurgical processing, is necessitated.Application of Enhanced Gravity Separators for Fine Particle
احصل على السعر
Minerals Free Full-Text Production of Vanadium
The renewable energy revolution calls for high-performing materials and makes metallic compounds like lithium, cobalt, nickel and vanadium more and more critical. Innovations contribute to inventions and developments like vanadium redox flow batteries for large-scale energy storage systems with numerous technological advantages. Potential 3.6.1. Falconbridge iron ore plant. The Falconbridge iron ore plant was operated between 1955 and 1972 and processed pyrrhotite concentrate via a sulfation roast-leach process to recover Fe in the form of a hematite product and base metals (Ni, Cu, Co) as a sulfide precipitate which is subsequently smelted (Rezaei et al. Citation 2017).Full article: The Direct Leaching of Nickel Sulfide Flotation
احصل على السعر