
A scale-up and design basis of continuous tube mills in cement
Introduction Mills are designed depending on users' requirements, e.g., the fineness of ground product, the production (or feed) rate and the environmental or spatial constraints for installation. The present study aims at establishing a basis to design the Mills are designed depending on users' requirements, e.g., the fineness of ground product, the production (or feed) rate and the environmental or spatial constraints A scale-up and design basis of continuous tube mills in cement
احصل على السعر
Optimization of continuous ball mills used for finish-grinding
The L/D ratio of the ball mill was varied in four steps of 1.75, 2.1, 2.79 and 3.49, and the ball charge filling ratio was varied in three steps of 15%, 20% and 25%. Tubular Rod Mills In Mineral Processing Design and Operations (Second Edition), 2016 8.3.1 Rod Mill Charge Rod mill charges usually occupy about 45% of the internal volume Mill Charge an overview ScienceDirect Topics
احصل على السعر
Tube mill drive systems a review Cement Lime Gypsum
In cement production, tube mills with multi-chambers are traditionally used in either open or closed circuit operations. The process of cement grinding basically includes a grinding [Show full abstract] performances of these cement grinding technologies, industrial scale data were collected from HPGR-ball mill, VRM, Horomill and multi Ball charge loading Impact of specific power
احصل على السعر
Design and application of liner of tube ball mill ResearchGate
By using process simulation under realistic conditions in a pilot grinding plant with a 0.725 m diameter x 2.5 m tube mill and scaling up the results to cement • Tube mill either open circuit- one compartment mill or closed circuit two compartment mill with small grinding media • Tube mill feed fineness 1800 3500 Operation of Tube Mills [PDF Document]
احصل على السعر
A Survey and Analysis on Electricity Consumption of Raw
is not energy-saving. Due to the high electricity consumption of the tube mill system, it has been gradually giving way to the vertical mill or roller press system at mill for cement The mill shell is divided by a diaphragm. Coarse grinding using big balls of up to 100 mm in diameter takes place in the first com- partment. The peripheral wear lining is designed as a lifting or activator plate lining which, with the large balls, achieves a high energy input for comminution. The transfer diaphragm allowsIndustrial Solutions polysius ball mills ThyssenKrupp
احصل على السعر
(PDF) Selection and design of mill liners
The one of main problem in cement industry is the continouse abrasion in lining plates of cement mill as a result of impact, abrasive and erosion by steel balls grinding media inside cement millThis paper deals with the operation of tube mills for grinding cement. For grinding different materials the same principles can be applied, adapting the parameters correspondingly to these conditions. Ø Ball charge for open circuit mill systems, where the ball charge in the second compartment must retain more material in the 2ndOperation of Tube Mills [PDF Document]
احصل على السعر
cement-mill PDF SlideShare
3.~ Nael Shabana 20103~ 6.0 Ventilation 7.0 Grinding and Generation of Heat 7.1 Heat Generation in Tube Mills 7.2 Cooling Procedures During Finish Grinding 7.3 Heat Balance for Mill Cooling 8.0 Cement Mill Specific Power Consumption 8.1 Calculation of Cement Mill Power Consumption 8.2 Calculation of the Specific Consumption of Water spray in the cement. mill is the widely used process to control cement temperature. The amount of water to be. sprayed per hour is calculated based on the heat balance calculations which comes to be around. 2100 lit/hr. Water spray system is designed to control the cement mill temperature by spraying.Cement Mill Water Spray System Report PDF Valve Pump
احصل على السعر
(PDF) A Survey and Analysis on Electricity Consumption
In the whole process of cement production, the electricity consumption of a raw material mill accounts for about 24% of the total. Based on the statistics of the electricity consumption of the rawThe energy consumption of the total grinding plant can be reduced by 20–30 % for cement clinker and 30–40 % for other raw materials. The overall grinding circuit efficiency and stability are improved. The maintenance cost of the ball mill is reduced as the lifetime of grinding media and partition grates is extended. 2.5.Energy-Efficient Technologies in Cement Grinding IntechOpen
احصل على السعر
Cement Mill Notebook PDF Mill (Grinding) Steel Scribd
Raw mills usually operate at 72-74% critical speed and cement mills at 74-76%. 3.2 Calculation of the Critical Mill Speed: G: weight of a grinding ball in kg. w: Angular velocity of the mill tube in radial/second. w = 2*3.14*(n/60) Di: inside mill diameter in meter (effective mill diameter). n: Revolution per minute in rpm. ~6~ Nael Shabana 2010Let us look back at the optimal ball charge in a mill. The necessary number of balls having the definite diameter N b in a mill should be proportional to grain number N having the definite diameters which they can grind: N b ~ N. (7) The number of grains of the material with determined diameters depends on the grain size distribution.THE OPTIMAL BALL DIAMETER IN A MILL 911
احصل على السعر
Operation of Tube Mills PDF Mill (Grinding) Hvac Scribd
1. INTRODUCTION. The proper operation of a tube mill system is the key to get the highest benefit out of a given installation. A prerequisite is that the system and the process are appropriately set-up. The operator has only a few adjustment possibilities, based on certain process values measured in the system and indicated in the control By using process simulation under realistic conditions in a pilot grinding plant with a 0.725 m diameter x 2.5 m tube mill and scaling up the results to cement grinding plants using semi-finishOptimization of continuous ball mills used for finish-grinding
احصل على السعر
(PDF) Investigating and comparing the effect of process
The results suggested that the operational capacity of cement mill of lines 1 and 2 when optimizing the process conditions increased by around 9.4 and 15%, and the blaine of the final product ofRaw mills usually operate at 72-74% critical speed and cement mills at 74-76%. 3.2 Calculation of the Critical Mill Speed: G: weight of a grinding ball in kg. w: Angular velocity of the mill tube in radial/second. w = 2*3.14*(n/60) Di: inside mill diameter in meter (effective mill diameter). n: Revolution per minute in rpm.(PDF) Cement mill notebook DOKUMEN.TIPS
احصل على السعر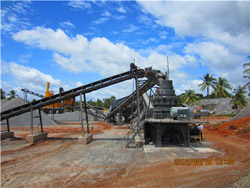
Ventilation Prediction for an Industrial Cement Raw Ball Mill
In cement mills, ventilation is a critical key for maintaining temperature and material transportation. However, relationships between operational variables and ventilation factors for an industrial cement ball mill were not addressed until today. This investigation is going to fill this gap based on a newly developed concept named “conscious laboratory Raw mills usually operate at 72-74% critical speed and cement mills at 74-76%. 3.2 Calculation of the Critical Mill Speed: G: weight of a grinding ball in kg. w: Angular velocity of the mill tube in radial/second. w = 2*3.14*(n/60) Di: inside mill diameter in meter (effective mill diameter). n: Revolution per minute in rpm. 7.Cement mill notebook PDF SlideShare
احصل على السعر
Tube mills for dry grinding. polysiususa
3 A 6.2 m x 20 m mill shell on its way from France to Malaysia. With an extensive range of grinding systems, consisting of x tube mills, x rod mills, x autogenous and semi-autogenous mills, x AEROFALL mills, x roller mills and x POLYCOM® high-pressure grinding rolls including x separators, x cement coolers, x dryers and x expert systems for The time history analysis is carried. function is used for ha. time step is 0.25 second for mill rotation and 0.0039. second for GMD motor. m = 2.7 mils at top of mill pi. litude calculated is 17.(PDF) DYNAMIC ANALYSIS FOR BALL MILL FOUNDATION
احصل على السعر
Operation of Tube Mills Internet Archive
mills and coal mills is similar and can be derived from this. Raw and coal mills include additionaily the drying aspects which have to be assessed. 2. NORMAL OPERATION Normal operation can be defined as the day to day operation of the mill system with a continuous mill output and a steady cement quality (fig. 1). Any common The specific power consumption is, as already said, influenced by the L/D ratio and the ball charge filling ratio of a ball mill. The investigations known from the literature were carried out with two compartment cement mills in the 1980s (Kuhlmann, 1985, Tätigkeitsbericht, 1991).Optimization of continuous ball mills used for finish-grinding
احصل على السعر
Cement grinding optimisation ScienceDirect
The “work horse” of the cement grinding plant is the two-compartment ball mill, commonly called the tube mill. Significant advances in model development were achieved in recent years (Benzer et al., 2001, Benzer et al., 2003) through research on industrial scale. The breakage and transport mechanisms are better understood as well
احصل على السعر