
Ball milling: a green technology for the
In particular, at a constant acid concentration, the yield of the isolated CNCs increased with longer reaction times, with optimal conditions after 4.5–5 The production capacity of the large-scale ball mill in the concentrator is a crucial factor affecting the subsequent separation and the economic benefits of the Enhancing the capacity of large-scale ball mill through
احصل على السعر
How to Improve the Production of Ball Mills? LinkedIn
Crushing the material into smaller particle size as much as possible before the materials into the ball miller, the solution is to configure a crusher with fine crushing In actual production, how can we effectively increase ball mill grinding efficiency? Seven tips will help you. 1.Increasing the grindability of raw ore Commonly, the grindability is...Seven Tips Increasing Ball Mill Grinding Efficiency
احصل على السعر
Effect of grinding media on the milling efficiency of a ball mill
Abstract. The size of grinding media is the primary factor that affects the overall milling efficiency of a ball mill (e.g. power consumption and particle size Increasing productivity in a ball mill involves optimizing several factors, such as the speed of rotation, the amount of grinding media, and the size of the material How to increase productivity in ball mill? LinkedIn
احصل على السعر
How to Improve the Production Capacity of Ball
One. Change the ball mill itself 1. Increase the cylinder volume in a scientific way: For the ball mill with same type and volume, decrease the thickness of the internal lining plate, so...The applications of mills are reviewed. The most used working regime of ball mills is described. The factors, affecting the milling process are examined. The Study of the factors increasing the quality and productivity
احصل على السعر
Ten Ways to Improve the Grinding Efficiency of
Here are ten ways to improve the grinding efficiency of ball mill. 1. Change the original grindability. The complexity of grindability is determined by ore hardness, toughness, dissociation andBall-mills are categorized into four types depending on the motion generated to produce momentum in grinding balls and act upon the material with various milling forces. These are planetary, tumbling, vibratory, and attrition mills. 3.1. Planetary ball mill. Planetary ball mills are simple and efficient in producing ground/pulverized material.Ball-milling: A sustainable and green approach for starch
احصل على السعر
Performance optimization of an industrial ball mill for
The ball mill consumes about 25-30% of the total energy in the beneficiation plant, and hence any improvement will improve the overall economics of the plant. However, the overall production cost per ton will decrease at higher throughput, due to the increase in production rate for the same level of energy consumption.Simulation result showed that, 10% capacity increase can be achieved with 16% material retained on 0.045 mm in the mill discharge when the mill was converted to a two-compartment mill. View ShowEnergy and exergy analyses for a cement ball mill of a
احصل على السعر
Ball milling as a synthesis method Aalto University Wiki
Introduction. Ball milling is generally known as a method to mix, blend, shape and reduce particle sizes. It can also be used as a mechanical synthesis method to produce materials that are milled to extremely fine powders. Several factors, like milling temperature, type of mill, milling speed etc. need to be considered when using ball millingAn increase of over 10% in mill throughput was achieved by removing the ball scats from a single -stage SAG mill. These scats are non- spherical ball fragments resulting from uneven wear of balls(PDF) Performance optimization of an industrial ball mill for
احصل على السعر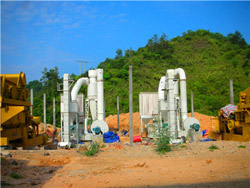
Ball milling as a mechanochemical technology for fabrication
Mechanochemical technique aims to strike a balance between defect formation via ball milling and size adjustment of a solid grain to nanoscale (<1000 nm) (Ullah et al., 2014).During the process, a high-energy mill is employed and a specific powder charge is placed along with a milling medium (Lin et al., 2017).The kinetic energy Ball mill balls. Ball mill balls are a type of ball used in ball mills, usually made of high-hardness materials such as steel, ceramics, hard alloys, etc. Ball mill steel balls is an important part of the ball mill, its main function is to carry out the grinding operation in the ball mill, and the material is crushed into the required size.Ball Mill Balls Manufacturing Of High Quality Ball Mill Ball
احصل على السعر
(PDF) Analysis of the efficiency of the grinding process in
It was determined that, approximately 12% circuit capacity increase could be achieved in composite cement production when ball mill, ball mill filter and air classifier power consumptions wereIt was also observed from the experimental results that in order to increase the milling efficiency of a ball mill, towards optimum production of material in the desired size class, there is a need to correlate the ball size and the feed size distributions. The ball mill, liners and grinding media employed were made from stainless steelEffect of ball and feed particle size distribution on the milling
احصل على السعر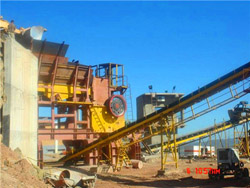
How to Improve the Production of Ball Mills? LinkedIn
Thirdly, the transformation of internal structure of ball milling machine is the most direct way to increase ball mill production; The disadvantage of the ball mills is very obvious at presentThe equation below shows the relationship between ball mill grinding efficiency and material fineness: Kd = G2/G1 = (d1/d2) X (1) *Note. Kd: the relative productivity of the mill; G1 & G2: respectively represent the mill output (T / h) when the feed particle size is d1 and d2; X: the index, which is related to material characteristics, productHow to Improve Cement Ball Mill Performance
احصل على السعر
On some problems of producing grinding media by cross
According to Cleary (2001), grinding in ball mills is still far from being effective due to high consumption of electrical energy and steel (grinding media). Currently, the cost of steel balls amounts to 45% of the total cost of grinding materials in ball mills (Lameck, 2005). The remaining costs include energy consumption and ball mill lining.2.1. Materials. The biochar was produced from the pyrolysis of OPEFB sourced from a local palm oil mill (Seri Bandar Palm Oil Mill, Malaysia) at a temperature of 500 °C for 25 min in a tubular furnace (Dentsply Ceramco, York, PA, USA) with a nitrogen flow rate of 258 mL/min; this is the modified method of biochar production used by Lawal High-Energy Ball Milling for High Productivity of
احصل على السعر
How Many Factors Affect Grinding Efficiency of Ball Mill?
01 Grinding concentration on ball mill grinding. Grinding concentration is one of the important factors affecting the working efficiency of ball mill.The influence of grinding concentration is mainly reflected in three aspects: the specific gravity of the slurry, the degree of adhesion of the ore particles around the steel ball and the fluidity of the slurry.Angewandte Chemie int. ed., 15. Oktober 2021. Source. DOI. Esc. Mechanocatalysis in a ball mill makes it possible to synthesise ammonia at much lower temperatures and pressures than those required for the Haber-Bosch process. This has been observed by a research team led by F. Schüth and S. Reichle from the Max-Planck Ammonia synthesis by mechanocatalysis in a ball mill Max
احصل على السعر
Effect of grinding media on the milling efficiency of a ball mill
The size of grinding media is the primary factor that affects the overall milling efficiency of a ball mill (e.g. power consumption and particle size breakage). This article tackles the lack of aThe ball mill Ball milling is a mechanical technique widely used to grind powders into fine particles and blend materials. 18 Being an environmentally-friendly, cost-effective technique, it has found wide application in industry all over the world. Since this mini-review mainly focuses on the conditions applied for the preparation andBall milling: a green technology for the preparation and
احصل على السعر
Ball Mill an overview ScienceDirect Topics
8.3.2.2 Ball mills. The ball mill is a tumbling mill that uses steel balls as the grinding media. The length of the cylindrical shell is usually 1–1.5 times the shell diameter (Figure 8.11 ). The feed can be dry, with less than 3% moisture to minimize ball coating, or slurry containing 20–40% water by weight.BALL MILLS ARE NORMALLY ABOVE 1.0 WHILST VSMs ARE LESS THAN 1.0 Vertical Raw Mill Production capacity increase & power decrease was realized by decreasing the Slatestone % and by IncreasingOptimizing Raw Mills Performance ; the Materials WAY
احصل على السعر
How to Improve the Production Capacity of Ball Mill?
1. Add fine crusher before the grinding stage can reduce the particle size of grinding materials, thus effectively reducing the load of the ball mill and improving the productivity of ball mill. 2
احصل على السعر